
Schematic with dimensions, displaying how the headplate and sleeve fit each other.
Headplate and light-blocking sleeve for 2P imaging
This system was designed to provide simple and reliable light shielding for 2-photon imaging in awake head-fixed mice (running on a 3D-treadmill with visual stimulation in our case). With this in mind, we optimized for the following criteria:
- No hand-made or improvised components that can add variability to the data quality of each experiment – so no putty, wax or tape.
- Simple connection between the animal’s headplate and the light shielding around the microscope lens, to prevent having to work close to the animal’s head, which can stress animals and impact task performance.
- Quick fastening mechanism (< 1 minute). Animals only have a limited time span for motivated, focused performance. We want to lose as little as possible of that time on setting up the imaging. Ideally, the time between putting the animal on the treadmill and beginning the first imaging sequence should be well below 10 minutes.
- Easy to ensure watertight seal with the skull to prevent leakage of fluid during imaging.
- Cheap and easy to replace/tweak if necessary.
We came up with a two-part solution. One is a circular headplate with a ring that rises up conically to fit around the microscope lens while providing a fluid reservoir for imaging with water-immersed objectives. The headplate has two connectors on the side that can be used for stable head fixation (similar concept to Poort et al. 2015 Neuron, Havenith et al. 2019 Scientific Reports). It is easy to implant on the skull, and then remains stable and watertight for months.
The second component is a light-absorbing conical sleeve which was designed to fit with an Olympus 20x objective, and can be lowered below the rim of the implanted headplate once the animal is head-fixed under the microscope. Since the sleeve is designed to fit snugly underneath the rim of the headplate’s cone, it doesn’t require any extra fastening mechanisms apart from lowering it past the headplate’s rim, making it extremely quick and easy to use. In our experience, lowering the sleeve all the way to the base of the headplate eliminates all stray light in recordings.
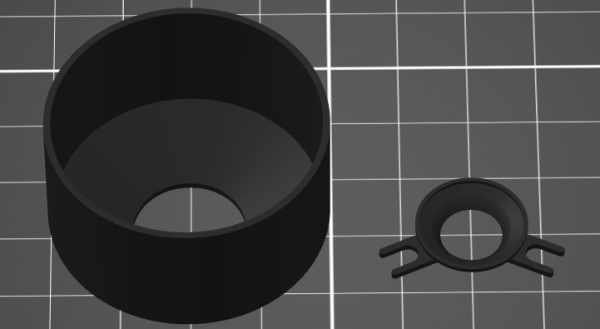
Parts rendering in slicer software. Left: sleeve. Right: headplate.
Manufacturing
While the headplate can be produced in a range of materials, we recommend machined, anodized aluminum, which is strong enough to ensure stable imaging-compatible head fixation while still being light. Anodizing the headplate adds a protective layer, can reduce light scattering, and adds electrical insulation to the rest of the system, which might be desirable for simultaneous electrophysiology. For test purposes, printing the headplate in a sturdy plastic can work well.
The sleeve should be made in an opaque plastic, preferably one that is matte/does not reflect stray light. For this part, some flexibility and ‘stickiness’ are desirable. The flexibility allows moving the objective in the XY plane (by at least a few 100 microns) without any effect on the headplate/sleeve seal. The stickiness makes the sleeve adhere to the objective. It can be moved manually, but stays in place otherwise. A material with these properties is TPU (thermoplastic polyurethane). We print the sleeve on an FDM printer with 200μm layer height, 100% infill.
Files
Copyright 3Dneuro 2020.
This source describes Open Hardware and is licensed under the CERN-OHL-S v2
You may redistribute and modify this documentation and make products using it under the terms of the CERN-OHL-S v2 (https:/cern.ch/cern-ohl). This documentation is distributed WITHOUT ANY EXPRESS OR IMPLIED WARRANTY, INCLUDING OF MERCHANTABILITY, SATISFACTORY QUALITY AND FITNESS FOR A PARTICULAR PURPOSE. Please see the CERN-OHL-S v2 for applicable conditions.
Source location: https://www.3dneuro.com/open-hardware